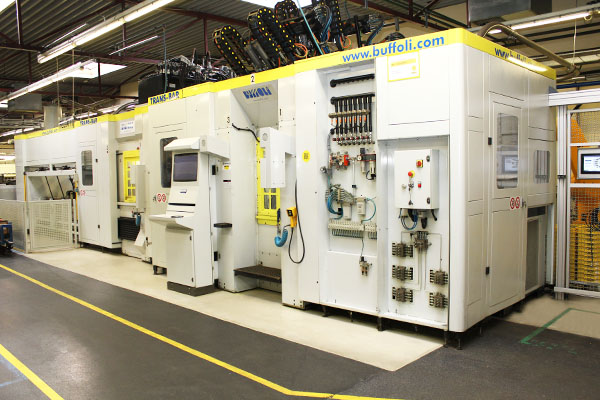
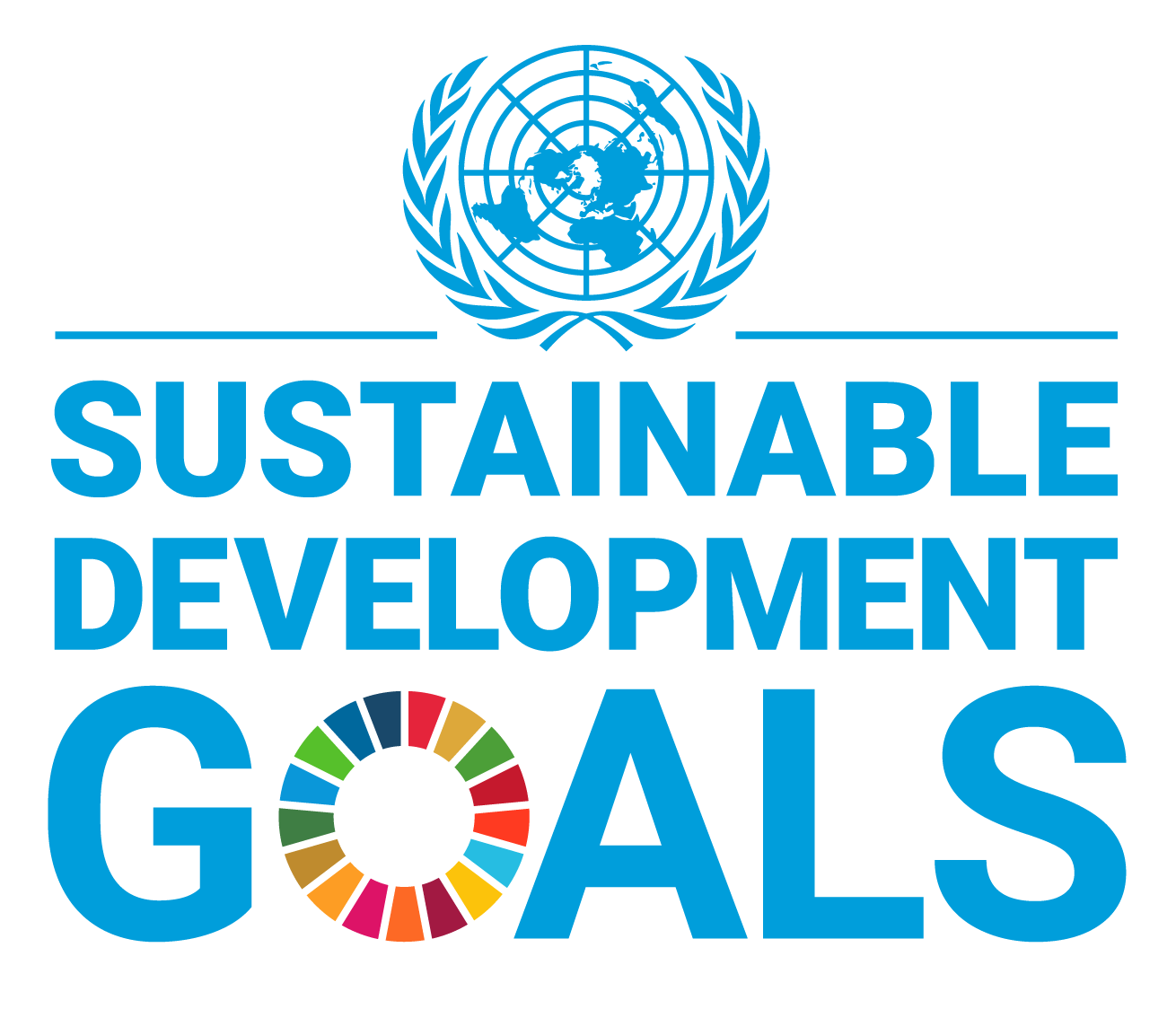
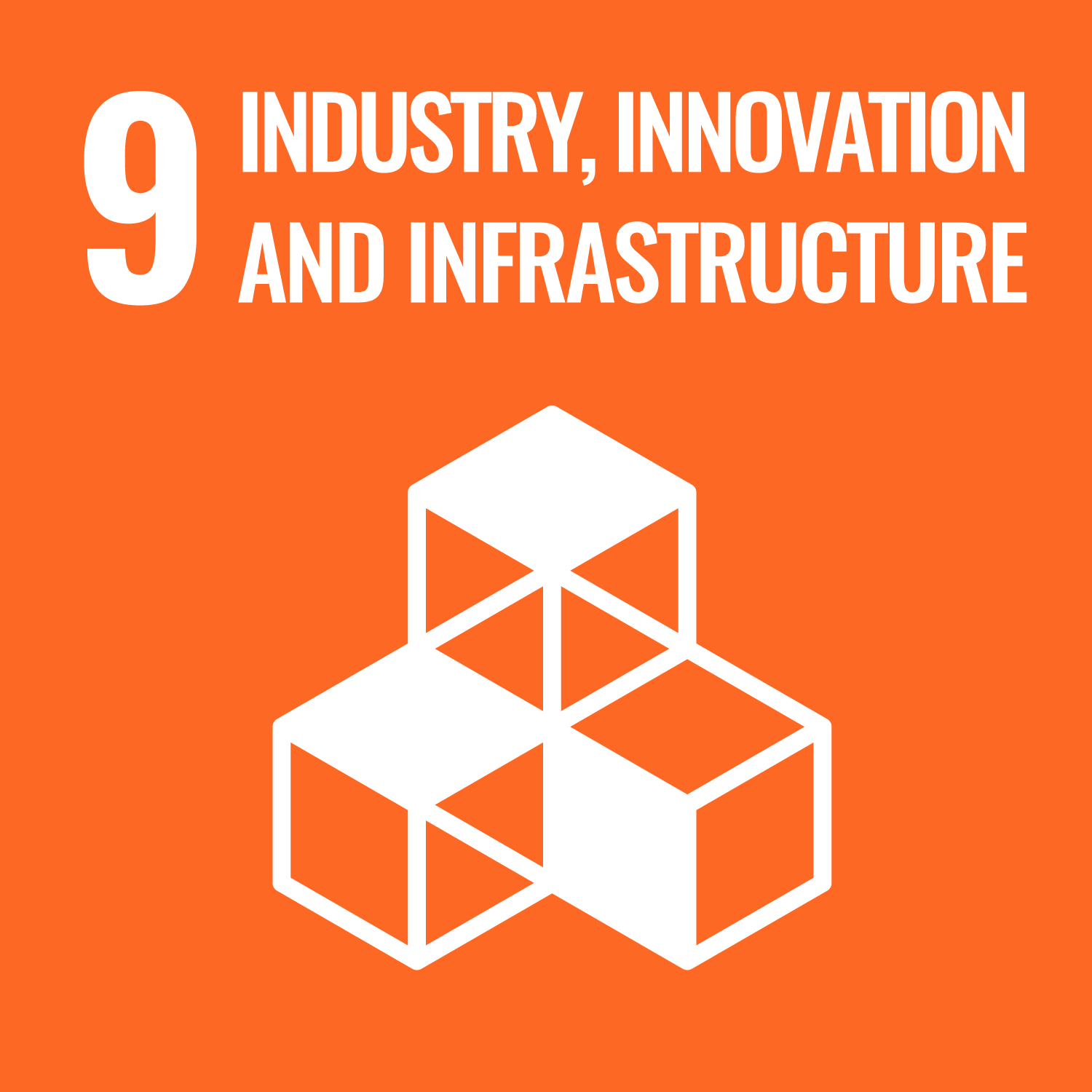
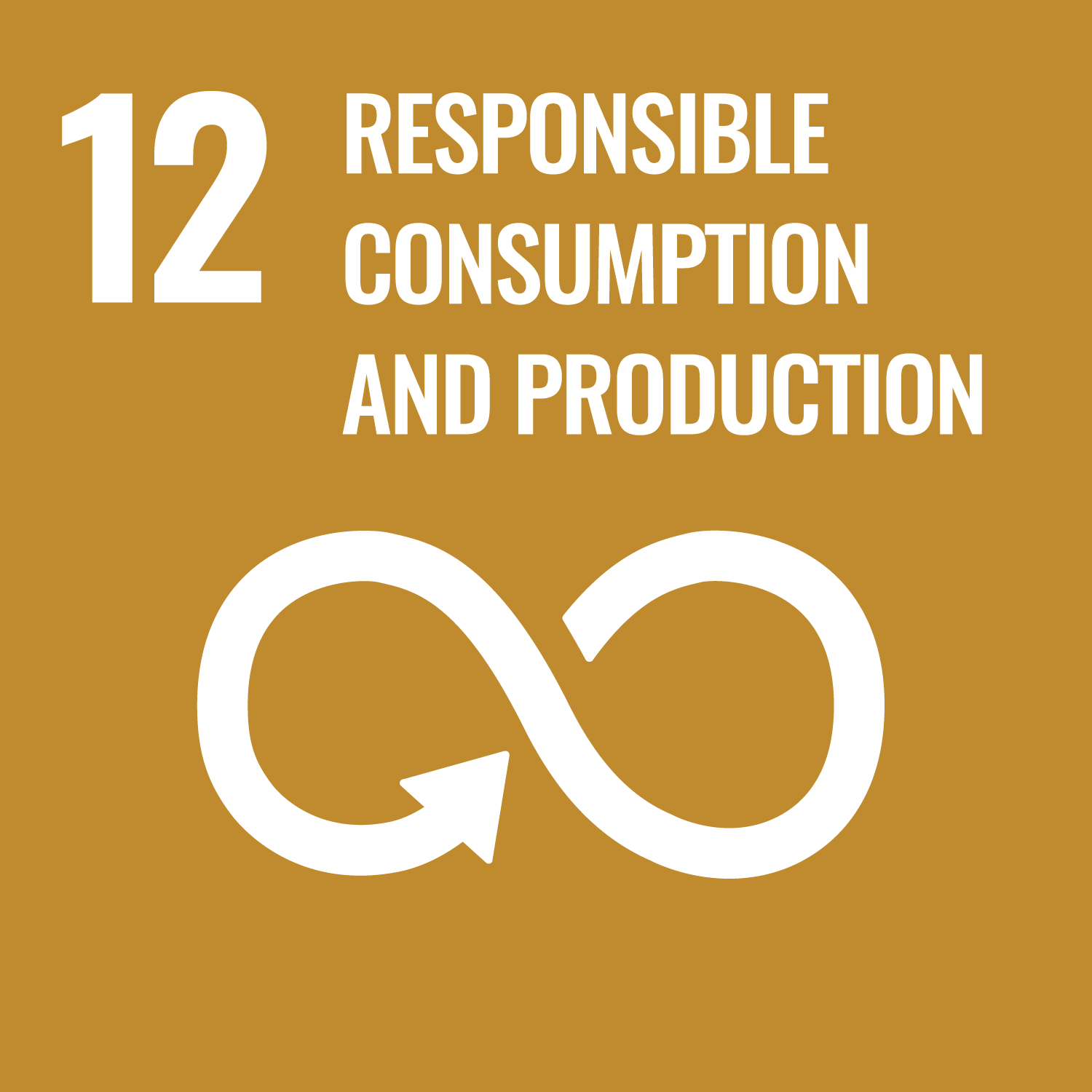
Producing without oil and emulsions …
The increasing energy consumption worldwide influences climate change. If oil is used as a lubricant in production, this means raw material consumption, environmental pollution and disposal costs. However, EVVA’s Clean Production (CP) protects the environment and resources because it works dry, i.e. it produces without oil or emulsions. The emulsions used in production do not contain oil. They consist of approx. 97% water, the rest is a non-hazardous chemical on which fungi can also grow.
… and without water
EVVA Clean Production is not only oil-free, but also 100% water-free. Cleaning the parts with chlorinated hydrocarbons (CKW) can thus be completely omitted.
Clean production share in relation to the entire machine fleet (headquarters):
3x more sustainable
Clean Production impressively demonstrates how well ecological, economic and social sustainability can complement each other.
Ecology:
EVVA introduced clean production machines many years ago to limit material consumption. In 2022, we were able to increase our CP share to 75% and in 2024 to 80% of the entire machine fleet, which is approximately 300 machines already using this technology to manufacture.
Since 2021, EVVA has commissioned several new clean production systems, e.g. for key milling, security cylinder housings and one for the production of high-quality locking cylinder cores - it was named “Constantin II” after a son of the owner family. This state-of-the-art Industry 4-0 system is perfectly prepared for networked applications. Processes are automated, such as assembly. “Constantin II replaces several previously used machines,” says project manager Johann Bunzengruber.
EVVA has invested several million euros in new CP systems since 2015. This saves us considerable amounts of resources:
One drop of heat is that a CP machine requires approximately 50% to 80% more electricity than a conventional oil-based installation (due to the cooling units and the higher compressed air requirement, measured by the compressed air consumption of the compressor control). But it can often replace not just one, but several conventional machines, such as our cylinder core systems. On average at EVVA, a single new CP machine replaces 3 to 5 systems previously used for the same purpose. A CP machine produces completely dry and does not require any of the usual downstream washing processes of the production parts to clean them of oil. Metal chips can also be recycled immediately without any cleaning. The higher power requirement is thus offset by high raw material savings and the avoidance of cleaning and waste.
Economy:
He who consumes less, also must buy less. In addition to the aforementioned ecological effect, our Clean Production saves around EUR 270,000 per year in purchasing and disposal at the current 80% share.
Another economic advantage: CP production enables a much faster production run of the components than with conventional machines (e.g. because the workpieces do not need to be de-oiled). For example, with a pin cylinder core in just 10 seconds - instead of the 30 and more seconds that the many machines used previously required.
Social aspects:
Working with oil can cause skin irritation. So the less needed, the better for the production staff.
Multiple award-winning
In recent years, EVVA has been awarded the City of Vienna's Environmental Award and the TRIGOS Sustainability Award for its sustainable, clean production innovation. Around half of our machines in the finishing and assembly areas were designed, manufactured and assembled by our in-house mechanical engineering department. Because there are often no suitable installations on the market, they have to be specially designed and manufactured to meet our quality requirements. EVVA is proud of this expertise.
How would you like to share?